A Comprehensive Overview to the Refine and Advantages of Plastic Extrusion
In the vast world of production, plastic extrusion becomes a very reliable and essential procedure. Translating raw plastic into continuous profiles, it provides to a huge selection of industries with its amazing adaptability. This overview intends to elucidate the detailed steps involved in this technique, the types of plastic suitable for extrusion, and the game-changing benefits it brings to the market. The occurring conversation guarantees to unravel the real-world effects of this transformative process.
Comprehending the Fundamentals of Plastic Extrusion
While it may appear complicated at very first look, the process of plastic extrusion is fundamentally simple. The procedure begins with the feeding of plastic material, in the kind of granules, powders, or pellets, right into a warmed barrel. The designed plastic is then cooled down, strengthened, and cut right into desired sizes, completing the process.
The Technical Process of Plastic Extrusion Explained
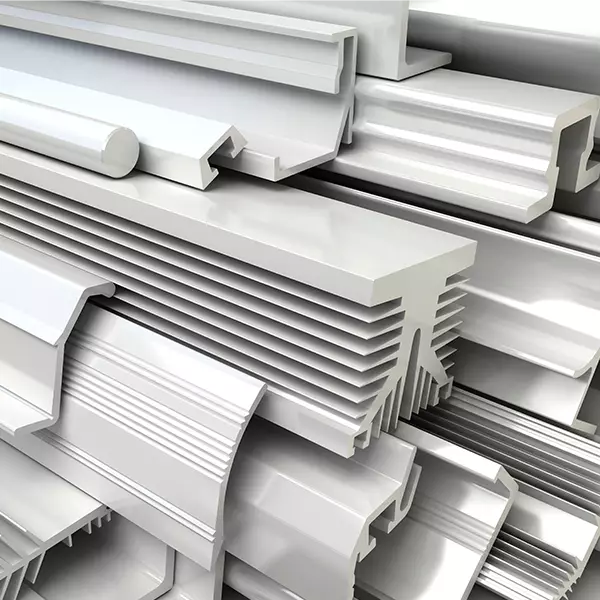
Kinds Of Plastic Suitable for Extrusion
The selection of the ideal type of plastic is a vital aspect of the extrusion procedure. Various plastics use special homes, making them extra fit to particular applications. Understanding these plastic kinds can dramatically enhance the extrusion procedure.
Comparing Plastic Extrusion to Other Plastic Forming Methods
Understanding the kinds of plastic ideal for extrusion paves the way for a broader conversation on exactly how plastic extrusion compares to various other plastic developing techniques. These consist of shot molding, impact molding, and thermoforming. Each method has its one-of-a-kind uses and advantages. Injection molding, for instance, is excellent for developing elaborate components, while blow molding is ideal for hollow objects like containers. Thermoforming excels at developing superficial or huge parts. However, plastic extrusion is unrivaled when it involves producing continual accounts, such as pipes, gaskets, and seals. It likewise permits a constant cross-section along the length of the product. Hence, the choice of approach mainly depends on the end-product needs and specifications.
Key Benefits of Plastic Extrusion in Production
In the world of manufacturing, plastic extrusion supplies numerous considerable benefits. One significant benefit is the cost-effectiveness of the process, which makes it an economically attractive manufacturing technique. In addition, this method provides premium item versatility and enhanced production rate, consequently boosting overall manufacturing efficiency.
Cost-efficient Production Method
Plastic extrusion jumps to the forefront as an economical production approach in manufacturing. In addition, plastic extrusion calls for less energy than standard manufacturing techniques, contributing to lower functional prices. On the whole, the financial advantages make plastic extrusion a highly appealing choice in the production industry.
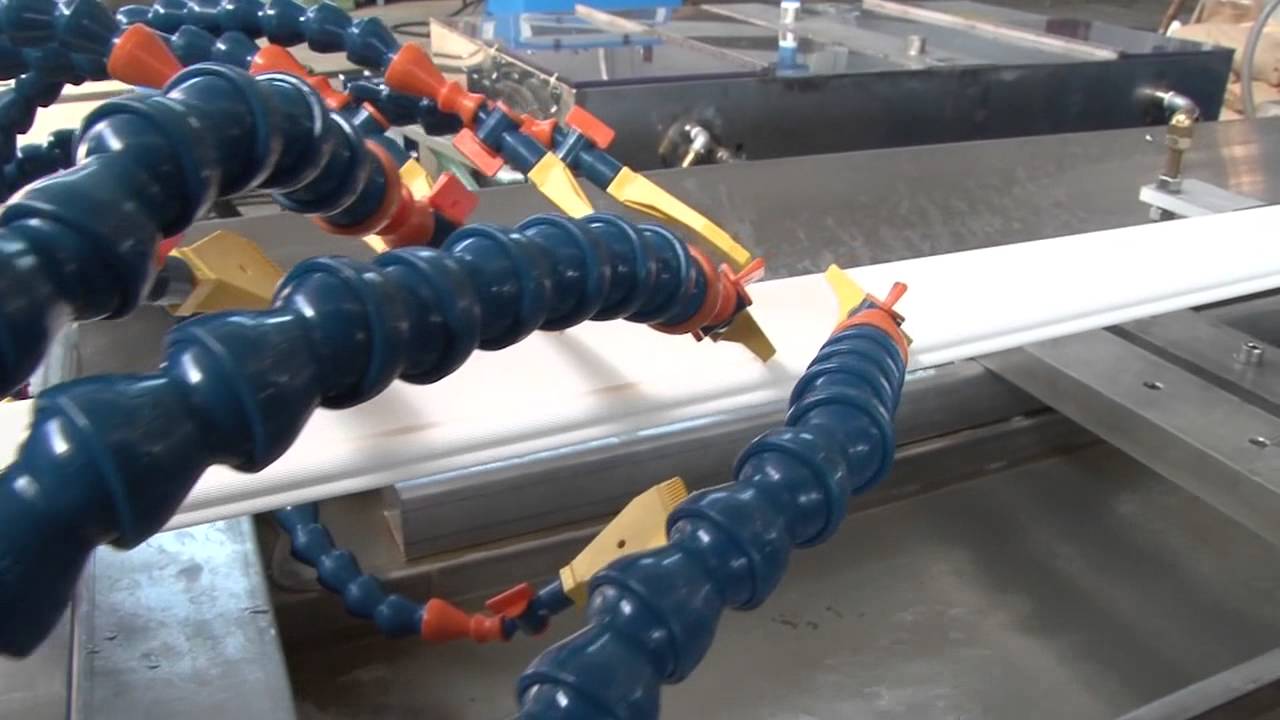
Superior Item Flexibility
Beyond the cost-effectiveness of plastic extrusion, another considerable benefit in producing lies in its premium product adaptability. This procedure enables for the creation of a wide range of products with differing designs, sizes, and forms, from simple plastic sheets to intricate accounts. The adaptability is attributed to the extrusion die, which can be personalized to produce the desired product style. This makes plastic extrusion an ideal solution for industries that call for personalized plastic elements, such as automobile, construction, and product packaging. The capacity to create diverse items is not only beneficial in meeting particular market demands yet likewise in allowing producers to discover brand-new line of product with marginal capital expense. Basically, plastic extrusion's product adaptability fosters technology while enhancing operational performance.
Boosted Manufacturing Speed
A significant benefit of plastic extrusion lies in its enhanced production rate. This production procedure enables for high-volume production in a reasonably brief time span. It is qualified of creating long, constant plastic profiles, which significantly minimizes the manufacturing time. This high-speed production is particularly useful in markets where large quantities of plastic parts are needed within limited target dates. Couple of other production processes can match the speed of plastic extrusion. In addition, the capacity to maintain regular high-speed production without sacrificing item top quality sets plastic extrusion aside from other methods. The boosted production speed, for that reason, not only makes it possible for producers to satisfy high-demand orders but additionally contributes to enhanced efficiency and cost-effectiveness. This helpful function of plastic extrusion has actually made it a preferred selection in numerous sectors.
Real-world Applications and Impacts of Plastic Extrusion
In the realm of manufacturing, the strategy of plastic extrusion holds profound value. The economic advantage of plastic extrusion, explanation largely its high-volume and cost-efficient outcome, has reinvented manufacturing. The market is constantly striving for innovations in biodegradable and recyclable products, indicating a future where the benefits of plastic extrusion can be kept without endangering environmental sustainability.
Final thought
To conclude, plastic extrusion is a extremely efficient and efficient technique of transforming raw materials right into diverse items. It provides numerous benefits over other plastic forming approaches, consisting of cost-effectiveness, high output, very little waste, and design adaptability. Its influence is greatly really felt in various sectors such as construction, automobile, and consumer items, making it a pivotal procedure in today's manufacturing landscape.
Delving much deeper into the technical procedure of plastic extrusion, it begins with the selection of the ideal plastic material. As soon as cooled, the plastic is cut into the great post to read called for lengths or wound onto reels if the product is a plastic movie or sheet - plastic extrusion. Comparing Plastic Extrusion to Other Plastic Forming Methods
Understanding the kinds of plastic ideal for extrusion leads the method for a more comprehensive conversation on how plastic extrusion stacks up against other plastic creating see here now techniques. Couple of other production procedures can match the rate of plastic extrusion.